The Aileron Bay Project.
Started: 11/11/1980
Finished: In Progress
One of the Comet's pioneering features was the use of hydraulic-only actuators
for all of the primary flight controls (ailerons, elevators, and rudder).
In other words, the Comet was a fly-by-hydraulics aircraft with no direct
linkage between these surfaces and the cockpit's yokes and rudder pedals.
Although hydraulic flight controls had been used for a time in military
aircraft, the Comet was the first civil transport to have them.
This was very brave engineering for a design concept that was essentially
complete in 1946. Hatfield engineers tell me that the major motivation
for doing this was the hydraulic system's natural damping of control surface
flutter.
There
were many special details, including totally new seal designs, and extensive
redundancy to avoid loss of control due to hydraulic failure. For instance,
the aileron control bay features servodyne cylinders massively sized for
the few pounds of force they have to deliver to the ailerons, plus there
are no less than six levels of system redundancy, all of which would have
to fail before the pilot lost control of the ailerons.
Incidentally, I have not been able
to find any record of hull loss or accident due to hydraulic failure.
The early systems in the MK 1 tended to leak and be messy, but with reasonable
attention, they did not fail. Given the historic significance of this
feature, we decided that the aileron control bay should be an important
part of the display. Although it was in truly terrible shape, all of the
parts had to be removed and restored to static display standards. The
plan was to completely rework all of the components and re-install them
to achieve a 'like new' appearance.
We
gained first access to the area during the general removal of most of
the aircraft's floorboards, including the compartment just aft of the
wing center section. This was done soon after the beginning of restoration,
in mid 1996. Work on the bay itself began in September 1999 with removal
of the bay's floor support structure.
Our crew then removed the compartment's smaller
components. Badly corroded items included:
1. The cabin pressure control system
2. Hydraulic reservoir and associated plumbing
3. Servodyne control and feedback cables, including those for the ailerons,
the rudder, and the elevators.
4. Complex (and very foul) cable tensioner assemblies
5. Backup electrical motor driven hydraulic pump assembly
6. Autopilot control input actuator
The very advanced corrosion we found made removal
of the two major servodyne assemblies extremely
difficult. After literally days of trying, we could not break free the
units, which have large magnesium casting frames, from the pressure hull-mating
surface. After much twisting, prying, jacking, and general brute force
effort, we were still not able to free them.
We eventually found that the magnesium frames had become so corroded that
they had become forcibly imbedded in the surrounding airframe. The only
recourse was to painstakingly work a broken off hacksaw blade around the
castings to free them. When the mass of magnesium oxide had been severed,
the assemblies slipped right off. After initial cleanup, the corrosion
damage was very evident.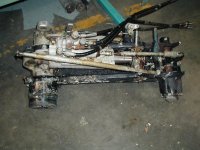
After removal, subassemblies were carefully photographed
to make a record of their original condition, assembly details, and the
correct type of finish. Each component from this bay has been given a
thorough and time-consuming restoration. For instance, the servodyne assemblies
had to be completely disassembled into more than a hundred separate parts.
Each
part was then cleaned and repaired as needed, then pickled (Aluminum parts
were Alodyned; Magnesium and steel parts received other chemical preparation.
Next, the parts were primed and painted. At the end of this process, the
finished parts were given a careful final color coat to reproduce the
original appearance.
After what seemed like eons, we finally have a completed aileron bay
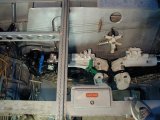
[Return]
|